Like the relationship with my mother in-law, decarbonising cement is bit dry and frankly hard to crack.
Cement’s chief property is to be extremely tough, no longer malleable after first impression and it softens ever so slightly over the decades.
It is the brutalist angular stamp we have left on planet Earth during the Anthropocene. From quarry to slab, from hospital to tomb, this calcium derivative is simply synonymous with human development.
In 2019 we poured enough of the stuff to cover the entire United Kingdom. It is estimated that the great pyramids weigh 5,750,000 tonnes. China pours that amount in under a day.
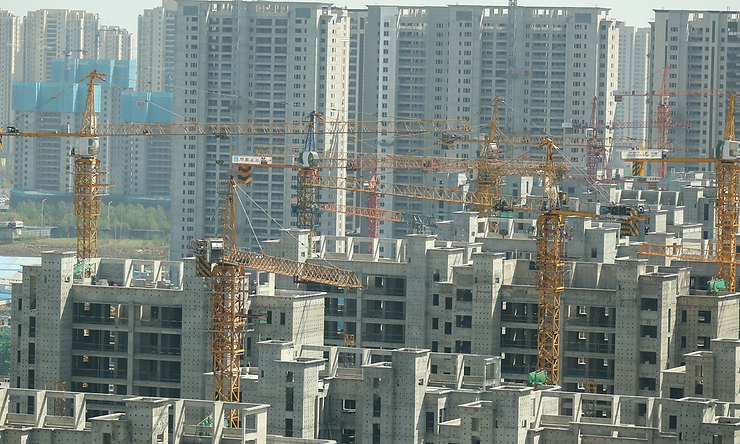
Getting out of our metropolis and urban sprawl, as shades of grey dissipate into green, one realises how desensitised we are to the material that rules our built environment. Reinforced with steel, we can build worlds that literally scrape the sky, dam enough water to keep billions from thirst and pave enough road to get us to moon and back more than a few times.
At 8% of the world’s emissions, cement needs a fix. As, like the relationship with my mother in-law, it is everywhere, holds our world together, and we simply could not do without it.
What’s the story with decarbonising cement?
Cast in history – a recipe for making cement
“[It]shall consist of at least two-thirds by mass of calcium silicates, theremainder consisting of aluminium- and iron-containing [compounds] … and othercompounds. The ratio of calcium oxide to silica shall not be less thantwo.”
The nearly two-thousand-year-old Roman Pantheon was built using cement and is a testament to cement’s durability. A composite of sand, aggregate (usually gravel or stones) and water mixed with a lime-based, kiln-baked binder, some researchers propose this as the most durable cement recipe cast to this day.
The Romans lost the recipe and after a hiatus on the earth’s crust, cement resurfaced in a big way as the bedrock of our industrial era. The modern industrialised form of the binder – Portland cement – was patented as a form of “artificial stone” in 1824 by Joseph Aspdin in Leeds.
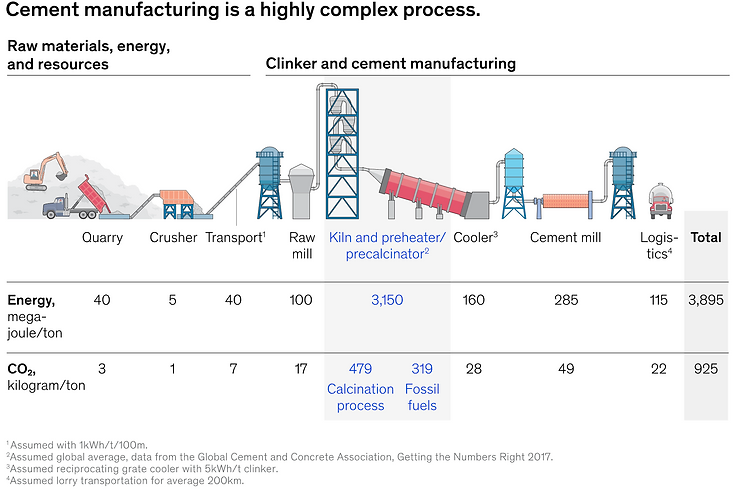
To make Portland cement, Calcium Carbonate (Limestone) is broken down in a thermodynamically intensive process, burned at temperatures near that of the sun’s surface, around 1450ºC. The raw calcium carbonate is fed into the system at the extreme temperatures along with clays and other additives termed “raw meal” at the preheater tower.
CO2 is released as a by-product during calcination, which occurs in the upper, cooler end of the kiln, or a precalciner, at temperatures of 600-900°C, and results in the conversion of carbonates to oxides or limestone to lime + carbon dioxide.
CaCO3 + heat = CaO + CO2
At higher temperatures in the lower end or furnace end of the kiln, the lime (CaO) reacts with components of the raw meal i.e. silica, aluminium and iron containing materials to produce minerals in the clinker, an intermediate product of cement manufacture.
The clinker is then removed from the kiln to cool, ground to a fine powder, and mixed with a small fraction (about 5%) of gypsum to create the most common form of cement known as Portland cement.
A corrosive carbonate’s climate conundrum
There are three key emitting parts of the Portland process.
- Heating limestone with fossil fuels at extreme temperatures to induce calcination and break bonds – c. 30% of CO2e
- Split of Limestone (CaCO3) into Lime (CaCO) and CO2, the emission of CO2 in the Calcination reaction – c. 60% of CO2e
- Transport and logistics of quarried and cementitious materials – c. 10% of CO2e
Geographically, cement has an outsized problem in Asia. China has poured more cement in the last 2 years than the US did over the whole 20th century. India is set to triple its building stock by 2050 and the cement sectors will see a near tripling of sectoral CO2 emissions, making it the single largest source of emissions in India.
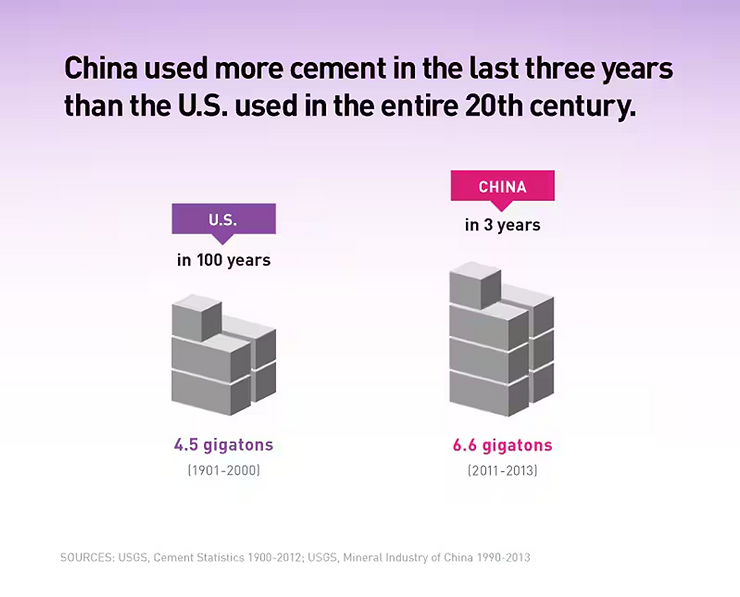
Globally, almost half a ton of cement is consumed per person per year, with cement production alone accounting for 3% of the total energy consumption and 8% of anthropogenic CO2 emissions.
No quick [set] fix
At Twynam we are scanning the globe for innovative approaches to decarbonising cement. Certainly, the market has scale, though where margin can be won sustainably is a question we struggle to answer. We have recently looked closely at materials innovation, new chemistries and carbon capture technologies. Unit economics is fundamental to the industry, and we struggle to envision a world bending on price for a green premium.
The pathways to decarbonising cement:
· Supplementary Cementitious Materials (SCMs): Replacing part of cement with materials like fly ash, slag, and natural pozzolans cuts emissions by reducing reliance on clinker, the most carbon-intensive part of cement. Use of SCMs or fillers to replace clinker is not new, and industry awareness of this approach is already relatively high. The advantage of replacing clinker with SCMs or fillers is that it doesn’t require changes in cement equipment or manufacturing processes. Regulations are also growing increasingly friendly toward the use of SCMs — the Netherlands allows producers to substitute up to 95 percent of the clinker in cements.
· Low-Carbon Cement: New types of cement like Limestone Calcined Clay Cement (LC3) and geopolymer cement reduce CO2 emissions by 30-80% through alternative chemical processes and lower clinker content. Historically, the industry’s held a deep-seated skepticism about the use of alternative binders which has presented a key challenge to reformulating cement recipes.
· CO2 Utilization: Injecting captured CO2 into concrete, where it mineralizes and strengthens the concrete, turning emissions into a resource. Researchers have recently developed an approach that achieves a CO2 sequestration efficiency of up to 45% and maintains an uncompromised concrete strength.
· Carbon Capture and Storage (CCS): Capturing CO2 directly from cement plants and storing it underground or repurposing it for industrial use offers a pathway to significantly reduce emissions. CCS in cement production faces challenges such as high costs, energy intensity, and technical difficulties with capturing CO2 at low concentrations, making it less efficient and economically viable. Additionally, issues with long-term storage and scalability hinder widespread adoption.
Some of the problems that we see are that cement’s a bulk product with raw inputs that are not only cheap but also reliable and abundant. It’s a recipe that has had thousands of years to perfect, and most of its climate impact comes from the very chemistry that makes it cement. The major challenge with alternative clinkers today is that materials that can partly replace limestone often have limited supply or are used in competing industries, which can impact cement’s cost.
Solutions will need to be as cheap and as strong as the incumbent, utilise existing supply chains, and tap into the quirks of the cement industry. It's a tough nut to crack, but with global cement emissions rivalling entire countries, the payoff could be massive - both for the planet and for investors willing to take the plunge.